Smart technology is being introduced to let Suzuki dealers pinpoint the location of every part they order from the firm.Thanks to a novel web-based system, dealers will be able to track the progress of all the 27 vehicles used to deliver the 8,000 units of stock sent out each day to the Japanese company’s franchised network.
Suzuki worked for 16 months with global supply management specialist Ceva Logistics to develop a track and trace system that is claimed will make Suzuki GB’s £16 million Milton Keynes headquarters parts centre the most efficient in the industry.
“We now have the ability to track anything from a single nut or bolt to an engine or chassis between here and its destination,” said parts and accessories division operations manager Andy Franks.
“We’re in the process of rolling out the GPS system to provide all 450 of our car, motorcycle and marine dealers with real-time and live data showing the location of assets in transit.
“After developing a paperless closed loop system to manage our 94,000 lines of stock, it seemed logical to extend the process and oversee the distribution within the network more effectively.
“It has already proved to be such a success that Suzuki is planning to use it at every other distribution centre around the world,” said Franks.
“We will also cut the time it takes to issue credits because parts returned will trigger an automatic payment on arrival.”
Smart technology tracks Suzuki parts
- By
- |
- 13 November 2008
- News
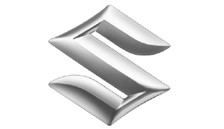
Login to comment
Comments
No comments have been made yet.